کاربرد آندهای فداشونده روی در صنعت نفت و گاز
اهمیت صنایع نفت و گاز در جهان:
نفت و گاز و مشتقات آنها از منابع ضروری در تامین انرژی مورد نیاز بشر می باشد. به نوعی زنجیرهی استفاده از نفت و گاز و تولید انرژی، تمام زندگی ما را وابسته به این صنعت نموده است. به منظور بهره برداری از این منابع عظیم و حیاتی و انتقال آنها در فواصل طولانی نیازمند استفاده از خطوط لوله غوطه ور در آب دریا و یا زیر سطح زمین و حتی در کف اقیانوسها می باشد. مشکلات خوردگی و پیامدهای فاجعه بار روی خطوط لوله اغلب به دلیل شرایط محیطی ایجاد می شود. خوردگی در خط لوله زیرزمینی گاز طبیعی و نفت مایع اشکال مختلفی دارد و برای مدیریت و تشخیص خوردگی به استراتژیهای خاصی نیاز دارد. یکی از این روشها، استفاده از آندهای فداشونده روی در سیستم حفاظت کاتدی می باشد.
در صنایع نفت و پتروشیمی حفاظت طولانی مدت از سکوهای نفتی دریایی، خطوط لوله سوخت و چاههای نفتی بسیار حائز اهمیت است. آسیبهای ناشی از خوردگی این سیستمها اثرات جبران ناپذیر و ویرانگری خواهد داشت. با بکارگیری آندهای فداشونده روی، ضمن حفاظت از محیط زیست می توان سوخت و انرژی مورد نیاز جهان را تامین نمود.
نقش آند فداشونده روی در حفاظت از سازه های نفتی و گازی:
خوردگی یک تهدید جدی برای مراکز فرآوری نفت جهت استخراج مشتقات نفتی به شمار میآید، دستگاهها و تجهیزات فلزی مانند مخازن ذخیرهسازی نفت، خطوط لوله، جداکنندهها وکلیه سازههای فلزی در معرض این آسیب قرار دارند .


یکی از انواع رایج خوردگی در فلزات، خوردگی گالوانیکی می باشد که ناشی از وجود اختلاف پتانسیل در فلز می باشد. این اختلاف پتانسیل نیروی محرکه در سلول الکتروشیمیایی می باشد که منجر به تخریب تدریجی این سازه ها می باشد. بنابراین به یک سیستم کنترل خوردگی موثر نیاز دارد. به منظور جلوگیری از خوردگی و حفظ یکپارچگی تجهیزات، موارد زیر باید اجرا شود:
- انتخاب مواد اولیه مناسب
- تغییر محیط
- کاربرد طراحی مناسب پوشش ها.
- حفاظت کاتدی
- طراحی مناسب
انتخاب بین موارد فوق معمولاً به ملاحظات اقتصادی بستگی دارد. با این حال، حفاظت کاتدی به طور گسترده مورد استفاده قرار می گیرد و راه موثری برای کاهش و کنترل خوردگی واحدهای فرآوری میادین نفتی محسوب می شود.
با توجه به پایین بودن مقاومت الکتریکی در آب شور، آند فداشونده روی مناسبترین و مقرون به صرفه ترین انتخاب جهت محافظت از سازههای به کار رفته در صنعت نفت و گاز می باشد. علاوه بر این، فلز روی دارای بالاترین ولتاژ الکتریکی منفی است و نسبت به فلزات دیگری همچون آلومینیوم و منیزیم، محافظت بهتری در برابر خوردگی ارائه می دهد.
شرکت کیمیاکاران کاوشگر کیهان کارون با بهره گیری از نیروهای متخصص یکی از بزرگترین تولیدکنندگان آند روی در اشکال متنوع و متناسب با نوع سازه و درخواست کارفرمایان صنایع نفت و گاز می باشد.
انواع سیستمهای مورد استفاده در کشتی ها برای جلوگیری از رشد رسوبات دریایی
رسوب زیستی یکی از مشکلات اصلی هر نوع کشتی در دریا است. رشد دریایی نظیر بارناکل و ماسل ها دلیل مشکلاتی نظیر کاهش کارایی کشتی، خوردگی و غیره بوده است.
با توجه به اینکه حذف چنین رسوباتی با استفاده از ابزارهای مکانیکی همیشه امکانپذیر نیست، به همین دلیل در کشتی ها از انواع سیستم های جلوگیری از رشد دریایی در کنار رنگ های ضد رسوب استفاده می شود.
انواع اصلی اقدامات پیشگیرانه مورد استفاده در کشتی ها جهت جلوگیری از رشد خزه عبارتند از:
سیستم آنتی فولینگ دوگانه (Anti-Fouling Systems)
دوز شیمیایی (Chemical dosing)
سیستم اولتراسونیک (Ultrasonic system)
الکتروکلرینیشن (Electro-chlorination)
سیستم آنتی فولینگ دوگانه:
یکی از رایج ترین سیستم های مورد استفاده برای مبارزه با رسوب زیستی در کشتی ها بکارگیری آندهای ضدخزه دوگانه است.
این سیستم از جفت آند، عمدتاً مس و آلومینیوم (یا آهن) تشکیل شده است. آندها در سی چست کشتی یا صافی نصب می شوند. با عبور جریان DC از آندهای مسی یونهایی تولید میشوند که با آب دریا در کل شبکه لولهکشی حمل میشوند و مانع از نشستن و تکثیر موجودات دریایی در سطح لوله ها می شود. از آند دوم برای جلوگیری از خوردگی سطح فلز استفاده می شود و یک کنترل پنل، خروجی هر یک از آندها را اندازه گیری و نظارت می کند.
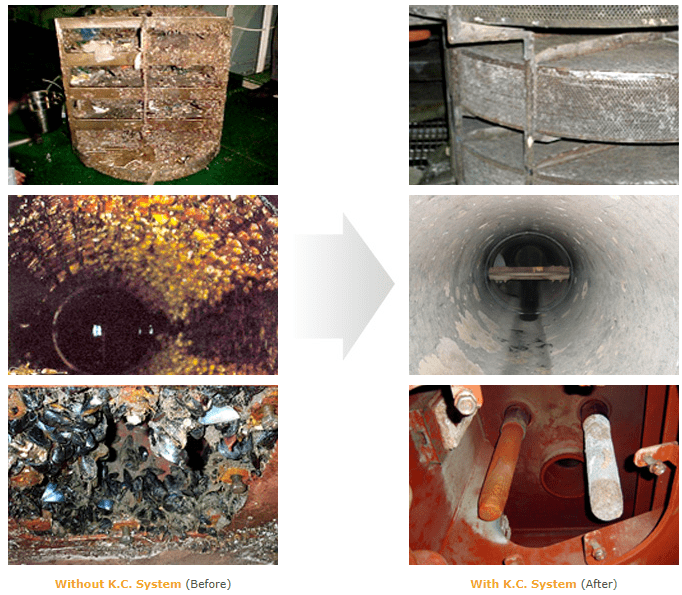
این سیستم همچنین از سوپاپ ها، کندانسورها، سیستم های خنک کننده موتور و تجهیزات جانبی محافظت می کند.
دوز شیمیایی
دوز شیمیایی نیز یک روش رایج است که برای جلوگیری از رشد دریایی در شبکه لوله کشی استفاده می شود.در این روش از مواد شیمیایی ضد رسوب مانند کلرید آهن در اطراف سازه استفاده می شود. این ماده شیمیایی لوله را با یک لایه آهنی محافظ می پوشاند تا از خوردگی جلوگیری کند.
سیستم اولتراسونیک:
این سیستم به عنوان یکی از موثرترین روش ها برای جلوگیری از رسوب زیستی شناخته می شود و کاهش رسوب زیستی تا ۸۰ درصد را نتیجه می دهد. طبق تحقیقات انجام شده، اولتراسونیک به دو شکل بر رسوبزدایی موثر است. امواج فرکانس بالا نه تنها زیستگاه را برای رشد خزه غیرقابل قبول می کند بلکه روی ارگانیسم های ۴-۵ میلی متری که قبلاً رسوب شده و به سیستم چسبیده اند نیز عمل می کند.
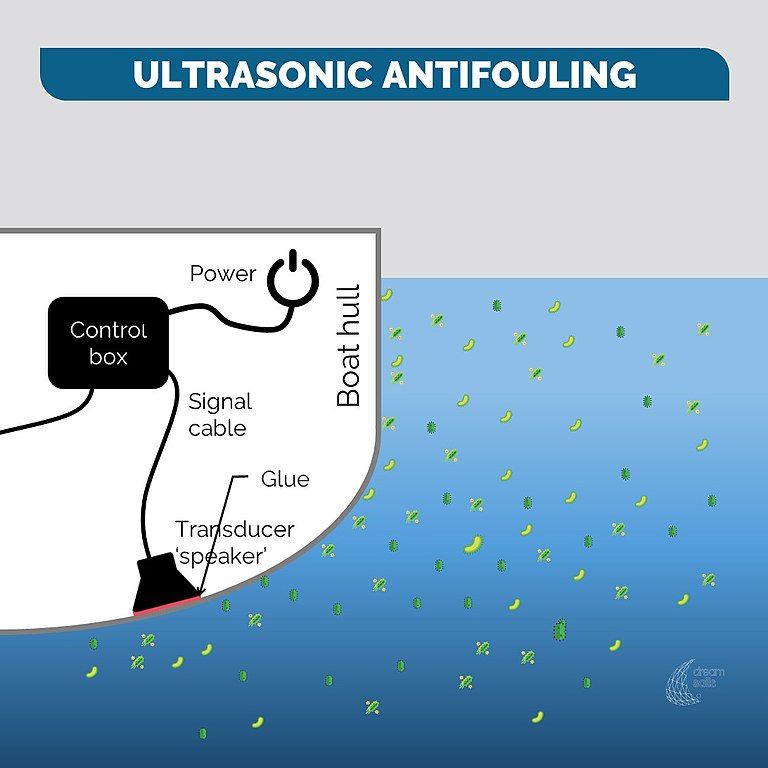
مزیت اصلی این سیستم غیر تهاجمی بودن و عدم تماس قطعه ای با آب دریا است. علاوه بر این، هیچ ماده سمی تولید نمی شود.
الکترو کلرینیشن :
الکتروکلرین روشی است که در آن از کلر برای تولید هیپوکلریت سدیم برای جلوگیری از رسوب استفاده می شود. تیتانیوم به عنوان ماده کاتد(کانداکتور بار) و تیتانیوم پوشش داده شده با ۱۰۰ میکرو اینچ به عنوان آند استفاده می شود. تیتانیوم یک عنصر الکتروشیمیایی خنثی در ولتاژهای مثبت کمتر از ۹ ولت است. ولتاژ آند/کاتد ۷ ولت نگه داشته می شود.
کلر در آندها همراه با عناصر دیگر تولید می شود و هیپرکلریت سدیم را تشکیل می دهد. مقدار زیادی گاز هیدروژن نیز تولید می شود که باید تخلیه گردد.
تأثیرات خوردگی در محیط زیست و صنعت
از دیدگاه محیط زیست، فعالیت خوردگی یک پدیده طبیعی است که برای حفظ تعادل در طبیعت ضروری است. خوردگی سعی می کند فلز را به پایدارترین شکل خود بازگرداند. با این حال، از دیدگاه مهندسی، خوردگی می تواند به عنوان یک حمله مخرب طبیعت به فلز دیده شود.
تخریب فلز و از بین رفتن قابل توجه مواد به دلایل شیمیایی یا الکتروشیمیایی در طبیعت منجر به ایجاد هزینه هایی چون هزینه نگهداری، تعمیر و تعویض و بازسازی می شود.
تاثیر خوردگی در زندگی مدرن دارای سه جنبهی اقتصادی، ایمنی و محیطی است. در ادامه به بررسی تاثیر این سه جنبه می پردازیم.
جنبه اقتصادی
تخریب زیرساختها با از بین رفتن مواد مورد استفاده در سازه هایی چون پلها، مخازن ذخیره سازی، خطوط لوله، سکوها و بسیاری از سازه های مهم دیگر منجر به زیانهای اقتصادی کلان می گردد. این زیان های اقتصادی می تواند مستقیم یا غیرمستقیم باشد. هزینه های مستقیم شامل هزینه جایگزینی سازههای خورده شده، تجهیزات و هزینه رنگآمیزی، نگهداری و نظارت بر سیستم های حفاظت کاتدی و همچنین استفاده از مواد اولیه گران قیمت با نرخ خوردگی پایین مرتبط میشود. فعالیتهایی که میتوانند در هزینه غیرمستقیم خوردگی نقش داشته باشند، ممکن است شامل بستن کارخانهها و تأسیسات برای تعمیر و نگهداری مورد نیاز به دلیل آسیبها و خرابیهای خوردگی باشد.
جنبه ایمنی
از بین رفتن مصالح سازه در اثر خوردگی نه تنها یک ضرر اقتصادی است، بلکه باعث ضعیف شدن سازه ها و کاهش قابلیت بهره برداری از آنها می شود. چنین سازههایی میتوانند به یک خطر ایمنی تبدیل شوند. خرابی سازه در اثر تداوم خوردگی در برخی موارد ممکن است فاجعهبار باشد و تلفات مالی و جانی به وجود آورد.
جنبه زیست محیطی
مواد، به ویژه فلزات، برای حفظ زیرساخت های توسعه تمدن مورد نیاز است. استخراج بیش از حد این منابع با ارزش، تهدید جدی برای محیط زیست خواهد بود. لذا یکی از مسئولیت های اولیه مهندسی ایجاد تعادل بین تقاضاهای روزافزون جوامع و منابع موجود درطبیعت می باشد. اگرچه خوردگی خود یک فرآیند بازیافت طبیعی است، اما پیشگیری از خوردگی منجر به کاهش آسیبهای وارده به محیط زیست میشود.
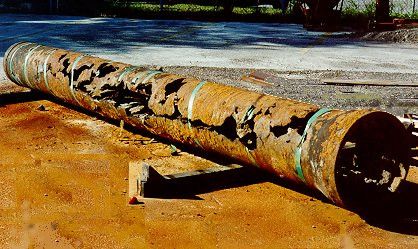
تأثیر اقتصادی خوردگی بر زندگی و تمدن ها احتمالاً محرک اصلی برای مطالعه خوردگی و توسعه اقدامات پیشگیرانه توسط صنعت است. دو جنبه دیگر مورد بحث در بالا تا حد زیادی در این فرآیند مورد توجه قرار می گیرند. بنابراین باید به دنبال راهی جهت کنترل هزینه های توسعه و از سویی اثرات زیست محیطی بود. مهندسان می توانند با مطالعه در مورد خوردگی و پیشنهاد اقدامات پیشگیرانه بهترین روش ممکن را ارائه دهند. لذا، مهندسان مسئولیت بزرگی در ایجاد تعادل بین نیازهای جامعه در حال توسعه و حفظ محیط زیست دارند.
در پایان به برخی از هزینه هایی که مستقیماً با خرابی های ناشی از خوردگی مرتبط هستند، اشاره میشود.
هزینه های خوردگی
- خسارات زیست محیطی
هیچ ارزش اقتصادی نمی تواند خسارت واقعی به محیط زیست ناشی از خرابی یک سازه را توجیه کند. این هزینه شامل هزینه تمیز کردن و جریمه های نظارتی و اقداماتی نیست که مستقیماً بر امور مالی یک شرکت تأثیر می گذارد بلکه شامل از بین رفتن منابع طبیعی و همچنین آلودگی های محیطی می باشد.
- اتلاف وقت و توقف تولید به دلیل آسیب خوردگی
توقف تولید به منظور توقف فرآیند خوردگی و انجام تعمیرات منجر به کاهش بازده تولید و درآمد میشود. اضافه شدن هزینه نیروی کار آماده به کار این هزینه را دوچندان می کند.
- وجود آثار خوردگی در محصول
در بسیاری از صنایع، آلودگی محصول به خوردگی میتواند منجر به مشکلات شدید کیفیت و از دست دادن شهرت تجاری شود و حتی گاهی ممکن است پیامدهای جدی برای زندگی و سلامت افراد داشته باشد.
- از دست دادن کارایی و افزایش سرمایه اولیه پروژه
در برخی موارد با پیشبینی خوردگی، بخشهایی از یک سیستم حفاظت کاتدی برای رسیدگی به خوردگی مورد انتظار طراحی میشوند. گاهی به دلیل عدم درک کامل از خوردگی و تاثیر آن، ممکن است یک سیستم حفاظت کاتدی بیش از حد برای راه اندازی و نگهداری سازه ها استفاده شود. این طراحی بیش از حد هزینه سرمایه پروژه را افزایش می دهد.
اندازه گیری مقاومت خاک به روش چهار پین ونر
یکی از مهمترین پارامترهای طراحی سیستم های حفاظت کاتدی برای سازه های مدفون در خاک ، مقاومت خاک است. آزمایش مقاومت خاک یک عامل بسیار مهم جهت ارزیابی خوردگی محیط نسبت به سازه های مدفون است. همچنین بر انتخاب نوع ، مقدار و ساختارآند تأثیر فوق العاده ای دارد. به علاوه انتخاب نوع بکفیل در بسترهای آندی به میزان مقاومت خاک بستگی دارد. بنابراین، کسب اطلاعات دقیق از شرایط خاک در محیط مورد نظر توسط طراح سیستم حفاظت کاتدی بسیار اساسی میباشد. نداشتن داده های کافی در مورد مقاومت خاک می تواند طراحی سیستم حفاظت کاتدی (سیستم CP) را بی اثر کند و در طول راهاندازی منجر به هزینه های زیادی شود.
هنگام انجام آزمایش مقاومت خاک ، عوامل متعددی که بر مقاومت خاک تأثیر می گذارند از جمله ترکیب خاک ، میزان رطوبت ، pH ، غلظت یون کلرید و سولفات را می توان مورد ارزیابی قرار داد.
در جدول زیر ارتباط بین مقاومت خاک و نرخ خوردگی ملاحظه میشود:
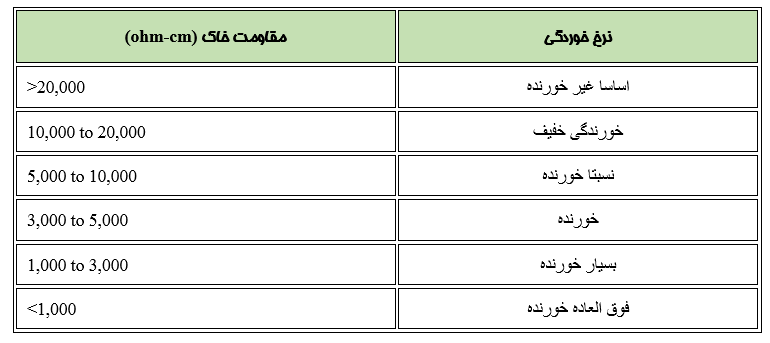
از آنجا که روشهای آزمایشگاهی برای تعیین مقاومت خاک معمولا پرهزینه و زمان بر است، از اندازه گیری های الکتریکی در همان محل استفاده می کنند. اندازه گیری های الکتریکی ارزان ، سریع ، قابل اعتماد و غیر مخرب هستند.
روش چهار پین ونر
در حالی که روش های مختلفی برای اندازه گیری مقاومت خاک وجود دارد ، متداول ترین روش آزمایش روش چهار پین ونر بر اساس استاندارد ASTM G57 است. این آزمایش از چهار پراب فلزی استفاده می کند که به فاصله یکسانی از یکدیگر داخل زمین قرار داده میشوند.
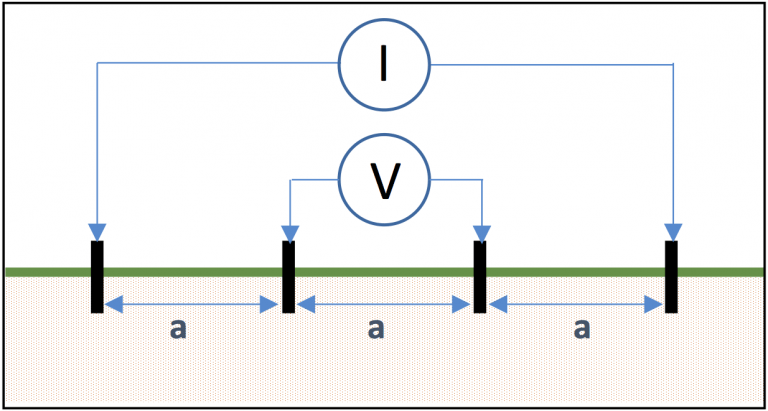
همانطور که در شکل ۱ نشان داده شده است پین های ابتدایی و انتهایی به منبع جریان (I) و پین های داخلی به ولت متر (V) متصل میشوند.
هنگامی که یک جریان معین از طریق پین های بیرونی در خاک تزریق می شود ، می توان از پینهای داخلی برای اندازهگیری افت ولتاژ ناشی از مقاومت خاک هنگام عبور جریان در مسیر بین پین ها استفاده کرد. سپس مقدار مقاومت R را می توان به مقدار مقاومت خاک با فرمول زیر تبدیل کرد:
ρ = 2 × π × a × R
که در آن “a” فاصله پین ها به سانتی متر است. مقدار ρ بدست آمده نشان دهنده متوسط مقاومت خاک در عمقی معادل فاصله پین ها است. بنابراین اگر پینها ۱.۵متر از هم فاصله داشته باشند ، مقدار بدست آمده معادل مقاومت متوسط خاک در عمق ۱.۵متر است.
برای طراحی سیستم حفاظت کاتدی ، معمولاً اندازه گیری مقاومت خاک با استفاده از این روش با فاصلههای مختلف پینها انجام می شود. برای قرار دادن آند در اعماق سطحی ، معمولاً کافی است که خوانش در ارتفاع ۱.۵متر ، ۳ متر ، ۴.۵ متر و۶ متر انجام شود. هنگامی که از آند در اعماق بیشتر استفاده میشود نیاز است که اندازهگیری مقاومت خاک در اعماق بیشتر مطابق با عمق پیش بینی شده انجام شود.
توجه به این نکته ضروری است که مقادیر مقاومت خاک حاصل از آزمایش چهار پین ونر نشان دهنده میانگین مقاومت خاک از سطح زمین تا عمق مورد نظر است.
حفاظت کاتدی سازههای بتن مسلح
حفاظت کاتدی برای جلوگیری از خوردگی میله های تقویت کننده در بتن
سالهاست که شرکتهای صنعتی و مهندسان برای محافظت از بتن مسلح فولادی در برابر خوردگی با هدف کاهش هزینه های تعمیر و نگهداری و تعمیر خوردگی بتن و افزایش عمر سازه تلاش کرده اند. عوامل اصلی خوردگی در بتن شامل نمک ، کلراید و یخ زدایی است. حفظ سازه های بتنی بزرگ مانند پل ها ، پارکینگ ها و اسکله های دریایی، عملی پایدار با مزایای زیست محیطی و عمومی است.
حفاظت کاتدی یک راه حل اثبات شده برای دوام بیشتر ساختارهای جدید و موجود است. تعمیر بتن به تنهایی یک راه حل طولانی مدت نیست زیرا ممکن است حتی پس از ترمیم لایه های ناشی از خوردگی، بتن هنوز آلوده به کلراید در اطراف میلگرد باشد. متأسفانه ، این وضعیت می تواند منجر به ایجاد محل های خوردگی ثانویه در اطراف منطقهی تعمیرشده گردد.
برای ارائه یک راه حل بلند مدت و اساسی ، روشهای مختلف حفاظت کاتدی وجود دارد. همه سیستم ها از این نظر که جریان محافظتی را به فولاد تقویت کننده می رسانند مشابه هستند ، اما مزایا و کاربردهای متفاوتی دارند. هر یک از این سیستمها می تواند سطوح متفاوتی از حفاظت و هزینه خوردگی را ارائه دهد. درک قابلیت ها و محدودیت ها به مهندسین و مالکان اجازه می دهد تا بهترین سیستم را برای حفاظت سازه پیاده سازی کنند.
سیستم حفاظت کاتدی تزریق جریان
سیستم تزریق جریان به کارگرفته شده شامل آندهای اکسید فلزی مختلط(MMO) مانند مش و روبان تیتانیوم ، سرامیک های رسانا یا پوشش های رسانا و یک منبع تغذیه DC خارجی برای تأمین جریان کافی به فولاد برای غلبه بر فعالیت خوردگی بتن است.
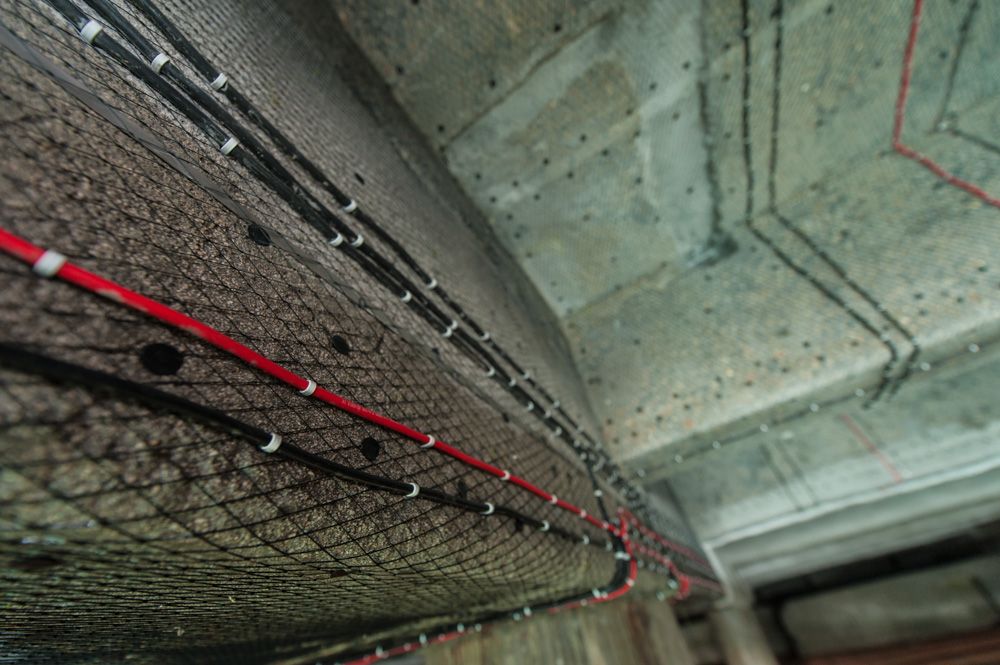
سیستم آندهای فداشونده
سیستم آندهای فداشونده از فلزاتی استفاده می کند که دارای اختلاف ولتاژ کافی نسبت به فولاد خورنده هستند و جریان محافظتی از آند در محیط الکترولیت به ساختار خورنده وارد می شود. معمولا از انواع مختلف آند فداشونده روی در برنامه های تعمیر بتن یا ترمیم بتن ، استفاده می شود. یک جریان الکتریکی با خوردگی آند فداشونده روی ایجاد می شود تا خوردگی فولاد تقویت کننده را کاهش دهد. آندها به صورت جداگانه بر روی فولاد تقویت شده با حفر یا سوراخکاری روی الگوی شبکه نصب می شوند.
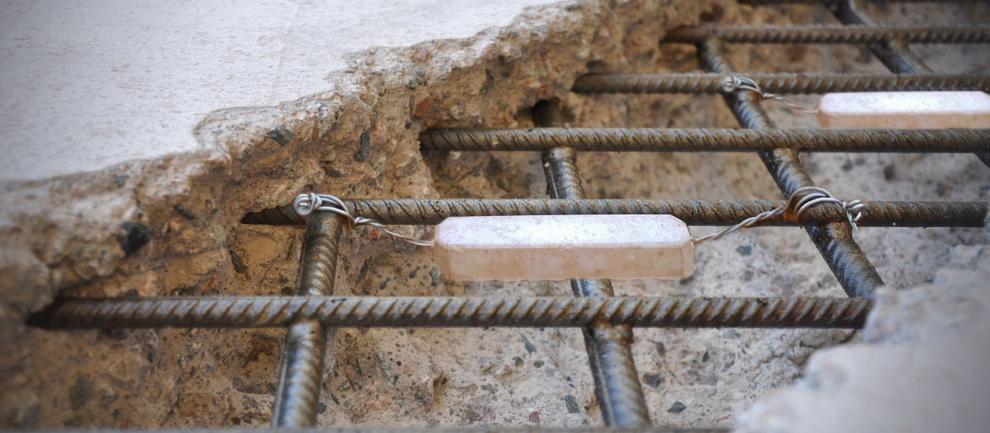
آندهای فداشونده همچنین برای محافظت از شمع های بتنی و فولادی در محیط دریایی استفاده می شوند. شمع های بتنی و فولادی در محیط دریایی در معرض خوردگی جدی قرار دارند. برای محافظت از شمع های دریایی ، از آندهای جکتی روی استفاده میشود.
شرکت کیمیاکاران کاوشگر کیهان کارون با بکارگیری دانش فنی و متخصصان مجرب آماده ارائه انواع آندهای فداشونده و آندهای تزریق جریان بر اساس درخواست کارفرما می باشد. جهت دریافت اطلاعات بیشتر می توانید با واحد فروش تماس بگیرید.
مبانی خوردگی سازههای بتن مسلح
خوردگی فولاد مقاوم در سازه های بتنی مانند ساختمانها ، پارکینگها ، سازه های دریایی بتنی ، بسترهای جاده ای ، عرشه پلها و زیرسازی پلها یک مشکل در سطح جهان است و منجر به ایجاد ترک ، نشتی از سطح و در نهایت ضعف ساختاری می شود. از طرفی تعمیر مناطق فرسوده که هزینه بسیاری نیز دارد تضمینی برای حل مشکل نمیباشد زیرا ممکن است شرایط برای ادامه خوردگی در سازه ایجاد شده باشد. این فرایند خوردگی می تواند پیامدهای ایمنی جدی داشته باشد ، به همین دلیل نظارت بر خوردگی با استفاده از یک روش دقیق و قابل اعتماد بسیار مهم است.
آزمایش پتانسیل نیم-سلولی تنها تکنیک پایش خوردگی استاندارد شده در استاندارد ASTM C876-15 است که برای تعیین احتمال خوردگی در میلگرد در سازه های بتنی مسلح استفاده می شود.
مبانی خوردگی بتن
در سازه های بتنی مسلح ، یک لایه محافظ طبیعی در اطراف میلگرد وجود دارد که از خوردگی آن جلوگیری می کند. با گذشت زمان ، کلرایدها (از یخ زدایی نمک ها یا قرار گرفتن در معرض دریاها) و یا CO2 به بتن نفوذ کرده و آن لایه محافظ را تجزیه می کنند. CO2 با کاهش میزان pH بتن تا زیر سطح پایداری لایهی محافظ، منجر به تجزیه موضعی آن می شود.
این فرایند خوردگی را می توان در شکل زیر مشاهده کرد:
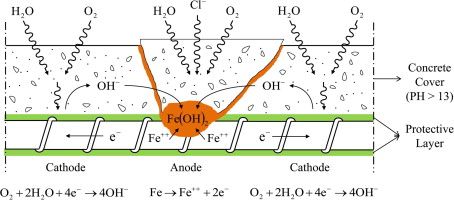
فلز (میلگرد) در محلول (موجود در منافذ بتن) واکنش می دهد و الکترونها را از آند (جایی که اکسیداسیون اتفاق می افتد) به کاتد (جایی که کاهش اتفاق می افتد) می دهد. یونهای مثبت تشکیل شده در سطح آند واکنش نشان داده و محصولات جانبی خوردگی ایجاد خواهند کرد. این واکنش الکتروشیمیایی یک اختلاف پتانسیل و در نتیجه یک جریان خوردگی بین مناطق آندی و کاتدی در سطح آرماتور فولادی ایجاد می کند. این جریان یا توزیع پتانسیل روی سطح بتن ، چیزی است که هنگام اندازه گیری پتانسیل نیم سلولی مورد توجه است.
تکنیک پتانسیل نیم-سلولی
شکل ۲ نشان دهنده سلولی است که در آن هر طرف به عنوان نیم سلول نامیده می شود. هر نیم سلول توسط یک الکترود در یک محلول (الکترولیت) نشان داده می شود و هر دو نیم سلول به یکدیگر متصل می شوند. از آنجا که یکی از الکترودها در مقایسه با دیگری تمایل بیشتری به خوردگی دارد ، آن الکترود (آند) اکسیده شده و الکترون آزاد میکند.
برای حفظ تعادل سیستم و تعادل بارها در الکترولیت ها ، تبادل یون ها از طریق پل نمک انجام می شود. اختلاف پتانسیل (ولتاژ) بین هر دو الکترود توسط ولت متر اندازه گیری می شود ، که میزان انحلال آند را نشان می دهد.
برای اعمال این مفهوم در بتن و تفسیر نتایج پتانسیل خوردگی ، یک الکترود مرجع با پتانسیل شناخته شده مورد نیاز است. به طور معمول ، برای کاربردهای بتن مسلح ، از الکترود مرجع مس/ سولفات مس (Cu/CuSO4) یا الکترود نقره/ کلرید نقره (Ag/AgCl) به عنوان الکترود مرجع استفاده می شود. با اتصال این الکترود مرجع به میلگرد و قرار دادن الکترود مرجع در سطح بتن ، می توان اختلاف پتانسیل بین دو نیم سلول را اندازه گیری کرد.
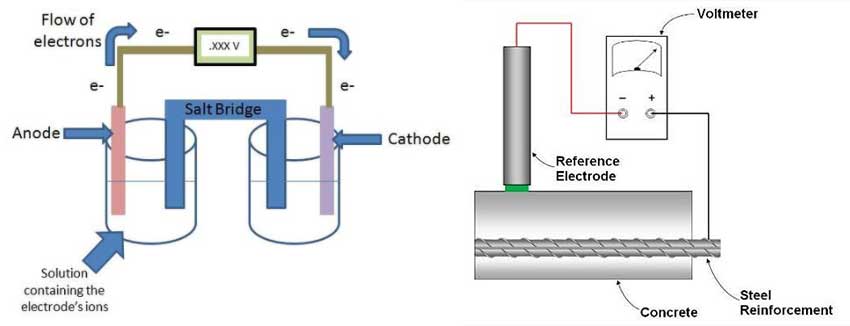
نحوه انجام این اندازه گیری و رابطه بین مقادیر پتانسیل اندازه گیری شده در استاندارد ASTM C876 ارائه شده است. در این اندازه گیری محدودیت هایی از جمله شرایط بتن (خشک یا مرطوب) ، وجود کلراید ، عدم وجود اکسیژن در سطح میلگرد (به دلیل اشباع شدن) ، ضخامت پوشش ، مقاومت بتن و دما وجود دارند که در تفسیر داده های بدست آمده باید در نظر گرفته شوند.