Types of backfill in cathodic protection system
Types of backfill
The type of backfill used in the cathodic protection system in ground substrates depends on the type of cathodic protection system used. Due to the fact that the cathodic protection system exists in two types of sacrificial anode systems and impressed current anode systems, so two types of backfill materials are also used.
Sacrificial anode systems
The sacrificial zinc and magnesium anodes used to cathodic protection of structures buried in the soil are sometimes packed in a linen bag with a backing material. These materials reduce the local corrosion of the anode by preventing the anode from coming into direct contact with the soil. It also prevents the anode from becoming passive by reacting with salts in the soil. The backfill used improves the performance of the anode by creating a low-resistance environment around the anode. These materials are generally a combination of three types of gypsum gypsum, bentonite and sodium sulfate, and the percentage of their compounds depends on the environment used.
The following table shows the types of backfills according to the IPS-M-TP 750 standard:
Impressed current system
Impressed current anodes for cathodic protection of underground structures are usually surrounded by a carbon backfill. The purpose of using this support is:
- By reducing the resistance of the environment around the anode, it leads to an increase in the amount of current produced by the anode.
- As the anode level increases, the amount of current increases.
- Reduce anode consumption rate and thus increase anode lifetime.
Carbon backfill according to IPS-M-TP 750 standard is available in three types of 80% metallurgical coke, 90% petroleum coke and 95% special petroleum coke.
The chemical composition of these three types of backfill is specified in the table below:
Coal coke is generally used in shallow horizontal substrates. Petroleum coke or special petroleum is used for deep wells.
- Published in Articles, Educational, Scientific
Mixed metal oxide anode (MMO) and its applications
What is a mixed metal oxide anode?
Mixed metal oxide anodes are made of a titanium substrate coated with mixed metal oxides. The coating is applied by several thermal processes on the titanium base to create a chemical resistant layer. Due to the inherent stability of titanium, this coating achieves the best performance of the anode by strengthening the conductivity of the anode.
MMO anodes have advantages such as very low consumption rate and high current capacity. Low anode consumption rate causes the anode dimensions to remain almost constant over the life of the anode. Therefore, these anodes are widely used in impressed current systems for land and marine structures.
MMO anode applications
MMO anode is used in cathodic protection system in different types of tubes, ribbons, meshes, wires and plates. These anodes can be used effectively in all environments such as soil, fresh water and saline water. Depending on the environment in which the anode is located, two types of coatings are considered for the anode. Iridium-tantalum coating is used in soil and fresh water and iridium-tantalium-ruthenium coating is used in saline water. The anode current capacity in soil, coke or fresh water is 100Amps \ m2 and in saline water is 600Amps \ m2.
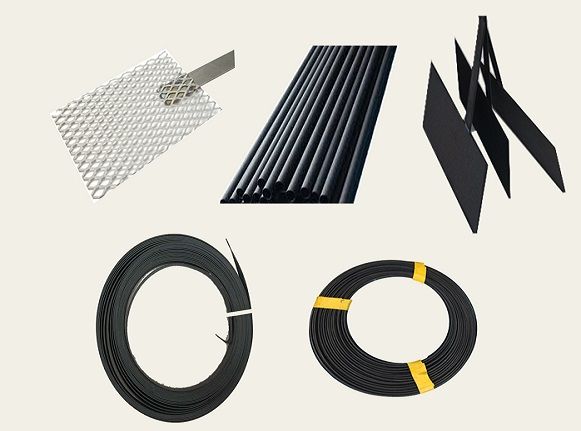
various type of MMO anodes
Types of MMO anodes
- Tubular Anode
Tubular anode is the most common type of MMO anode used in cathodic protection systems. The titanium of this anode is manufactured according to ASTM B338 Grade1 standard. Tubular anodes are usually used as strings in deep wells.
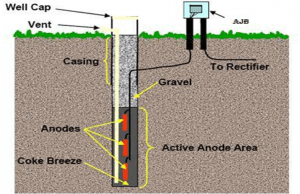
cathodic protection of deep wells by tubular mmo anodes
- Ribbon Anode
The titanium base of these anodes is manufactured according to ASTM B265 Grade1 standard and uses iridium / tantalum mixed metal oxide coating. This type of anode is used to protect the external bases of aboveground storage tanks. Ribbon anodes are suitable for connection to titanium conductors by spot welding to create a network under the tank that also provides a uniform distribution of current.
- Mesh Anode
Mesh MMO anodes are used in cathodic protection systems of reinforced concrete structures. Titanium mesh anode base like ribbon anode is produced according to ASTM B265 Grade1 standard and the anode quality is checked according to NACE TM0294 standard.
- Wire Anode
Titanium wire anode is an ideal cathodic protection product for protecting the bottom of tanks, submarines and pipelines. This type of anode is made of high grade titanium with a mixed metal oxide coating and has a lifetime of more than 50 years.
- Plate Anode
These types of anodes are designed as rectangular or circular plates for use on ships and vessels.
- Published in Articles, Educational, Scientific
Protection of water heater against corrosion
Maintenance of water heaters using a sacrificial anode
The use of water heaters in industry as well as in homes in various dimensions and shapes is essential. Therefore, its maintenance is very important. The water heater may run loudly over time as sediment builds up inside. This deposit may be due to natural minerals in the water or substances that result from corrosion of the sacrificial anode or the tank itself.
In a water heater, the sacrificial anode is visible as a rod that slowly erodes over time. The sacrificial anode is made of magnesium, aluminum or a combination of zinc and aluminum. The water in the tank causes corrosion of the inner steel of the tank by creating an electrolytic reaction. To protect the steel, a magnesium or aluminum rod anode is placed in place. After the anode corrodes, the tank steel begins to corrode and the tank fails.
Replacement time of sacrificial tank anodes
To protect the tank steel against corrosion, the sacrificial anode of the tank should be replaced every 3 to 5 years, depending on the type of tank. The warranty period of the tank can be used to determine the time of replacement of the anodes. If the anodes are not replaced in time, the tank will continue to work, but over time, the tank steel will corrode and tank replacement will be inevitable, which will cause a lot of damage.
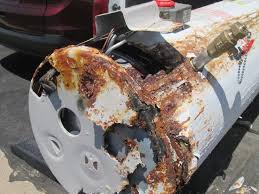
water heater tank corrosion
How to place the sacrificial anode in the tank
The sacrificial anodes are usually screwed to the top of the tank for easier access. Note that sometimes the length of these bars is long and you have to have enough space to take them out. Therefore, sometimes it is necessary to remove the tank to replace the sacrificial anode.
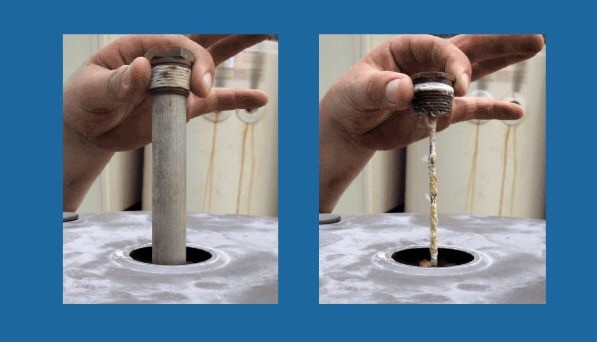
Water heater anode
What type of sacrificial anode is used in the tank?
The sacrificial anode type is usually recommended by the manufacturer. Aluminum sacrificial anode, although it may cost less, has a higher corrosion rate than magnesium anode. Also, in addition to making noise, the aluminum poured into the tank pollutes the water in the tank. Therefore, be careful never to use hot water from the tank for drinking or cooking. The most common sacrificial anode in water heater tanks is the magnesium sacrificial anode.
- Published in Articles, Educational, Scientific
Cathodic protection of pipelines
The role of cathodic protection of pipelines in the oil and gas industry
One of the main and very costly problems in large industries such as gas, oil, petrochemical, shipping, etc., is the corrosion of metal structures.
In the oil and gas industry, carbon steel pipelines are used to transport hydrocarbons from jackets to production platforms and storage tanks, and enter refineries through pipelines. Carbon steel pipelines are the safest and least expensive way to transport large volumes of hydrocarbons over long distances.
Fuel and water transmission pipelines and other structures buried in soil or submerged in water, due to their metallurgical conditions, are in a state of corrosion and after a while, the performance of the structure is disrupted.
Corrosion in the oil and gas industry dramatically increases the overhead costs of plumbing operations due to the replacement of worn equipment and damage to adjacent equipment. Therefore, it is necessary to use a proper protection system to prevent corrosion.
Corrosion control mechanism in cathodic protection of pipelines
Corrosion control mechanisms in oil and gas pipelines are mitigation measures to eliminate or reduce corrosion to prevent pipeline failure and related consequences such as crop failure, environmental pollution and potential accidents.
Five control mechanisms to minimize pipeline corrosion and cathodic protection of pipelines that must be considered during the design and construction of pipelines include design, material selection, coating, cathodic protection, and chemical protection.
Designing
One of the important factors in corrosion control is design. Proper design of a steel pipe increases the life of the structure. Gaps, steel geometry, sharp edges, welded joints, and pipeline connections such as flanges, valves, and pipe supports are often subject to local corrosion due to fluid penetration and dissolution.
In addition, these environments have poor coverage due to inaccessibility or sensitivity to coverage failure. These factors contribute to corrosion and should be carefully considered during the design phase to limit corrosion.
Material selection
The choice of materials is very basic in terms of engineering design to reduce corrosion. The choice of material depends on the environmental conditions such as the fluid being transferred, the temperature, the pressure and the electrolyte in which the pipe is placed (water or soil). Also in flange joints, piping and general joints where it is possible to pair metals of different materials, to prevent galvanic corrosion, care must be taken in determining the material.
Due to its good mechanical properties, availability and low cost, carbon steel, despite its low corrosion resistance compared to other corrosion-resistant alloys, is the main material for pipeline transmission.
coating
One of the main and simplest methods of protecting pipelines is coating. A suitable coating prevents direct contact of the outer surface of the tube with the surrounding environment and thus prevents the flow of ions through the electrolyte, thus limiting corrosion.
There are different methods and types of coating and the choice of its type depends on the type of material selected:
- Painting
Painting is used in environments where the equipment is only exposed to air and no electrolyte is available.
- Coating
The main types of coatings for coating structures that are exposed to electrolytes are strong coatings such as polyethylenes, bitumen and polypropylene.
- Lining
Lining the surface of the structure with rubber sheets.
- Cladding
coating one metal with another.
- Cathodic Protection
Using a cathodic protection system along with coating is an effective way to prevent corrosion of pipelines.
There are two general methods for cathodic protection of pipelines:
- Sacrificial anode system
- Impressed current anode system
In cases where the length of the pipeline is very long and in the presence of stray currents, an impressed current system is used to protect the pipeline.
Chemical protection
Chemical protection includes corrosion inhibitors, Oxygen purification system, and biocide in a chemical process.
In the chemical process, biocide is injected into the system, liquid or water to kill microorganisms such as reduced bacteria that increase corrosion under microbiological effects with sulfide. Oxygen scavenging chemicals are injected into the water to deoxygenate to reduce the severity of the corrosion and ultimately achieve adequate cathodic protection of the pipelines.
- Published in Articles, Educational, Scientific
Cathodic protection of underground storage tanks
Corrosion of underground storage tanks
Underground storage tanks are generally in contact with materials such as soil and sand. The electrochemical reaction between the tank and the surrounding soil (electrolyte) leads to tank corrosion. The small voltage difference on the steel surface causes a current to flow from one part of the tank to another. Corrosion occurs where current flows into the soil (electrolyte). This part in the galvanic cell is called the anode. Where the flow from the soil enters the reservoir is the cathode and corrosion does not occur.
Prevention of tank corrosion (cathodic protection of underground storage tanks)
An outer cover as well as a cathodic protection system are used to protect the underground tanks from corrosion. A suitable outer cover can protect more than 99% of the tank surface. But since there is no complete cover, in addition to the outer cover, a cathodic protection system must be used to protect the tank from corrosion. The cathodic protection system converts the tank into a cathode by applying an external current and protects it from corrosion. In cases where the amount of current required to protect the structure is small, sacrificial anodes are used. For large structures such as large diameter pipelines, an impressed current system is used.
Magnesium sacrificial anode for cathodic protection of underground storage tanks
Magnesium sacrificial anode is the most common sacrificial anode used in cathodic protection of underground tanks. Magnesium anode can protect underground tanks in any soil. To reduce the electrical resistance of the anode to soil, a magnesium anode is usually used inside a linen bag with backfill material that is a combination of gypsum plaster, bentonite and sodium sulfate. Magnesium anode is produced in two types of standard and high potential. High potential magnesium anode is used in soils with a resistance of about 10,000 ohm-cm. Based on the dimensions of the tank and the soil resistance in which the tank is located, the number and dimensions of the required anodes are determined. The two most common sizes of magnesium anodes to protect underground reservoirs are 17-pound and 32-pound anodes. The anodes are installed at a suitable distance and depth from the tank. The anode wire is connected to the top of the tank with a low-resistance electrical connection. All connections are covered with waterproofing.
In terms of cathodic protection of underground storage tanks, the technical and engineering department of Tavanazob Sana’ati Kavir Company is ready to provide consulting services for which you can contact us.
- Published in Articles, Educational, Scientific
What is an impressed current cathodic protection system?
What is a impressed current cathodic protection system and how does it work?
For cathodic protection in large structures, the use of cathodic protection system of sacrificial anodes may not be appropriate. The number of sacrificial anodes required to provide sufficient current to protect the structure against corrosion may be excessive or impractical. To control this, an external energy source is used to help conduct electrochemical reactions. are Impressed current cathodic protection system is a type of system that is usually used in cases where high flow requirements required to protect against corrosion or control needs to be increased. In impressed current cathode protection (ICCP) systems, the current required for protection is supplied from an external source of electrical energy supplied by a DC regulated power supply called a transformer. ICCP systems for corrosion protection are ideal for many structures, such as underground pipelines, storage tanks, large ships, and offshore and offshore structures.
How does a impressed current cathodic protection system work?
The impressed current cathodic protection system consists of one or more reference electrodes and several ICCP anodes, all connected to the same power supply. The reference electrodes adjust the required output current unit on the anodes by measuring the electrical protection potential of the environment in which the structure is located. Adjusted current prevents the corrosion process from occurring. In this method, unlike the sacrificial anode method, where the anodes were negative, the anodes are more positive than the structure. The positive pole of the power supply is connected to the anode and the negative pole is connected to the structure. Therefore, the positive ions inside the electrolyte return from the anode to the metal in question. Depending on the electrolyte in which the structure is located, the applied voltage must be such that it can withstand sufficient current intensity for all parts of the device that is cathodically protected. Provide. A properly installed, commissioned, and serviced ICCP system can last for 25 years or more.
impressed current anodes
The cathodic protection system consists of two types of anodes: the sacrificial anode and the impressed current anode.
A impressed current anode uses an external power source known as a “rectifier” to create a high potential difference between the protected surface and the anode. The anodes used are generally made of graphite, cast iron, titanium alloy and silicon iron. Today, the most common type of impressed current anodes are MMO anodes, which are found in various sizes and shapes such as wires, rods, tubes, plates and strips. The choice of the type of impressed current anodes to protect the structure from corrosion depends on the environment in which the structure is located. For example, ribbon MMO anodes are used to protect the bottom of tanks.
Impressed current anodes have advantages over sacrificial anodes, including:
- They have higher flow efficiencies.
- Less anodes are needed to protect the structure.
- Reduce the initial cost.
- Published in Articles, Educational, Scientific
- 1
- 2